Procesos Sidelurgicos
Se denomina de esta manera a la serie de pasos consecutivos que nos llevarán desde una materia prima como el mineral de hierro y el carbón de coque, hasta un producto final como el acero.
PROCESO POR ALTO HORNO
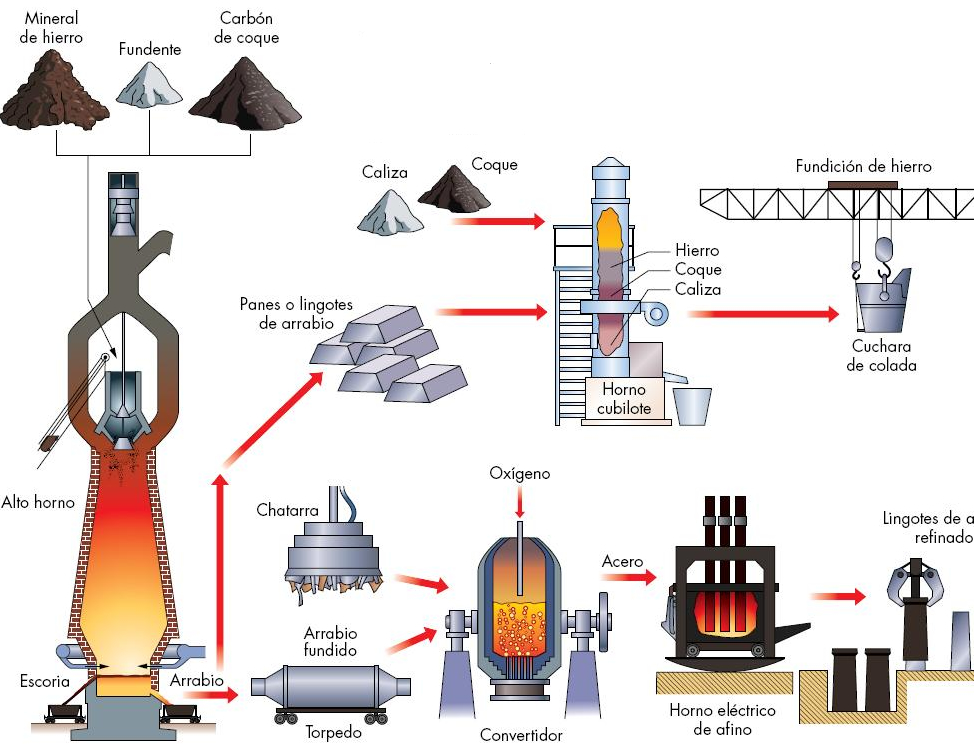
-
Como se observa en el siguiente imagen la producción se inicia cargando las materias primas (mineral de hierro, carbón coque y piedra caliza) por la parte superior del alto horno inyectando aire precalentado a aprox. 1.100ºC en la base del horno, lo que quema el coque generando altÃsimas temperaturas que funden el mineral y liberan gases que permiten separar el hierro del mineral. La piedra caliza a esas temperaturas se convierte en cal y captura parte de las impurezas, especialmente azufre y forma una escoria que flota sobre el mineral fundido. El material resultante de este proceso se denomina arrabio y contiene aún importante proporción de carbono e impurezas que se reducen en las etapas subsiguientes.
-
El arrabio es transportado al horno convertidor de oxÃgeno donde se le adiciona una parte de material de chatarra (aprox. 25% de la carga) y, mediante una lanza enfriada por agua, se le inyecta oxÃgeno puro a presión, generando temperaturas de 1.650ºC. En estas condiciones, el oxigeno se combina con el exceso de carbono en forma de gas y quema rápidamente otras impurezas que terminan flotando como escoria.
-
El proceso se completa con la desgasificación removiendo los gases producidos durante el proceso (oxÃgeno, hidrógeno y nitrógeno), lo que se logra mediante dos procesos posibles (desgasificación por flujo o en la olla de colada).
-
Finalmente, el acero fundido se vierte desde la olla de colada dentro de un depósito en forma de embudo desde el que fluye -a una velocidad regulada- dentro de un molde con superficie de cobre refrigerado por agua cuya forma hueca interior corresponde a la forma deseada de los llamados productos semi terminados: tochos, palanquillas y planchones. Los tochos y palanquillas son de sección cuadrada (comúnmente de 150mm por lado) y difieren en el largo en que se corta.
PROCESO DE REDUCCION DIRECTA
-
el horno de reducción directa es alimentado por la parte superior con mineral de hierro generalmente en forma de pellets inyectándole un gas reductor rico en monóxido de carbono e hidrógeno que reacciona con el óxido de hierro removiendo el oxÃgeno y convirtiéndolo en hierro metálico, que puede ser producido en forma de hierro esponja o en briquetas, las que posteriormente son procesadas en el horno eléctrico al arco.
Por su parte, las acerÃas, basan su producción en hornos eléctricos que, en vez de usar el oxÃgeno puro como combustible para generar las altas temperaturas requeridas, funden chatarra (o proporciones de hierro de reducción directa) creando un arco eléctrico entre los electrodos y la carga metálica.
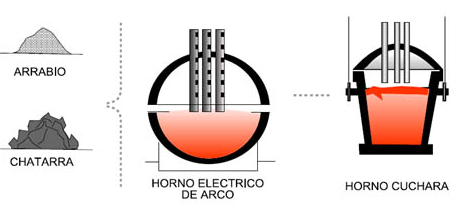
LAMINACION
-
La laminación del acero consiste en transformar los productos semi terminados reduciendo su sección hasta secciones deseadas, con el consiguiente alargamiento. En general, los tochos y palanquillas dan origen a la familia de los productos largos, en tanto los planchones dan origen a productos planos. El proceso de laminación en caliente se hace altas temperaturas y, tiene efectos no sólo sobre la dimensión de los elementos sino también sobre la estructura granular del acero, mejorando la dureza, resistencia y ductilidad. Entre otros efectos menos deseados de la laminación en caliente cabe mencionar la oxidación (cascarilla de laminación) y la consecuente imperfección de las tolerancias dimensionales. La laminación en frÃo se hace a temperatura ambiente y otorga a las planchas y flejes un acabado liso de la superficie, alta precisión dimensional y propiedades mejoradas (aumenta la dureza y resistencia aunque reduce la ductilidad)
